Obsolescence
PCB Reverse Engineering
Case Study
Ref. AMS-CS-4700529
Type: | Obsolescence, C&I Reverse Engineering |
Scope of supply: | Design, prototype, manufacture, test & qualify (Reverse Engineering) |
Market Sector: | Nuclear Power Generation |
Background
The Original Equipment Manufacturer (OEM) of a key piece of instrumentation used by the client was found to no longer manufacture or support the item. The instrument comprised an ultrasonic gap sensor, locally mounted head amplifier module and a remote mounted controller module. The sensing probe part of the instrument was considered to be in good working order but the electronic PCBs in the modules were showing signs of ageing, becoming less reliable and posing an increasing operator burden.
AMS were contracted by the client to reverse engineer the electronic modules making sure to minimise the differences between the original and new PCB so as to avoid needing to conduct a lengthy and expensive Engineering Change and requalification exercise.
Scope
The scope of supply for this project included:
- Obtaining obsolescence statement from OEM
- Managing an industrial electronics design sub-contractor to reverse engineer the PCB
- Producing new PCB design documents including Bill Of Materials
- Production and testing of a prototype
Outcomes
The outcome of the project was that AMS was able to successfully deliver a reverse engineered and fully tested prototype, thus paving the way for supplying production runs in the future. Furthermore, the design was sufficiently similar to the original to enable the Item Equivalency Evaluation method of ‘qualification’.
The project deliverables included:
- Design package to meet client requirement specification
- Item Equivalency Evaluation (IEE) at electronic component & complete PCB level
- Test reports proving functional equivalency with the original electronics
- Provision of tested & qualified electronic equipment
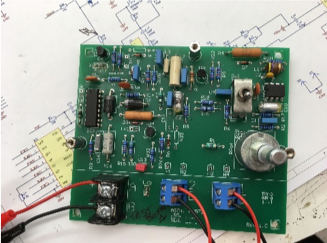
Key Skills Utilised
AMS were engaged with on this project due to having a reputation for Working with Appropriate Rigour (WAR), understanding the client’s procedures and having the SQEP resource to undertake the work.
Familiarity with the instrumentation to be reverse engineered and a close working relationship with the electronics design sub-contractor were also key enablers for this project.
Related
Documentation
13331
Obsolescence brochure
AMS-CS-4700529
PCB Reverse Engineering Case Study
Related
Case Studies
Replacement CCR Hardwire Fire Alarm System
EDF Energy – Hinkley Point B
AMS provided a detailed design for a replacement hard wired fire alarm system for Hinkley Point B Nuclear Power Station.
Superheater Overpressure Instrumentation Replacement
EDF Energy – Dungeness B
AMS was tasked to find a suitable modern replacement for the two signal isolators and the power supply based upon an item equivalency evaluation.